Each impoundment’s design, operation and closure plans contain mitigation and control measures to:
- Eliminate or avoid impoundment risks as much as possible.
- Quickly detect, minimize and contain the consequences of these events or conditions.
- Identify and address potential impacts on neighboring communities.
Typically, both tailings and residue storage facilities are constructed of earthen embankments, or dikes, forming an enclosure. The mine and refinery by-products are deposited into the enclosure in a slurry form and dried over time. Some impoundments are kept at their original height, with the perimeter embankment constructed to full height before deposition begins. Others are raised over time by methods described below, by depending on the type of tailings or residue being stored, and the method of deposition used. The methods for raising bauxite tailings and alumina residue storage dikes usually fall into one of the following categories:

Downstream: This method raises the impoundment height downstream from the initial dike which is built from borrowed fill materials.

Centre line: Successive raising occurs in such a way that the axis of the dike remains in the initial position and coincides with the initial dike axis.

Upstream: Successive levels of the containment dike are founded on the tailings or slurry previously discharged and impounded.
Closure and Remediation
To minimize our impact on communities and the environment, we aim to progressively close and rehabilitate our tailings and residue storage areas.
Our current impoundment closure strategy incorporates long-term planning and has the following main objectives:
- Aim for the beneficial reuse of bauxite residue and mine tailings and/or use process changes to eliminate the need for storage.
- Minimize impacts on the surrounding environment, including preventing leachate discharge and providing water treatment options.
- Pursue compatible land uses at closure, such as farmland and light industrial areas.
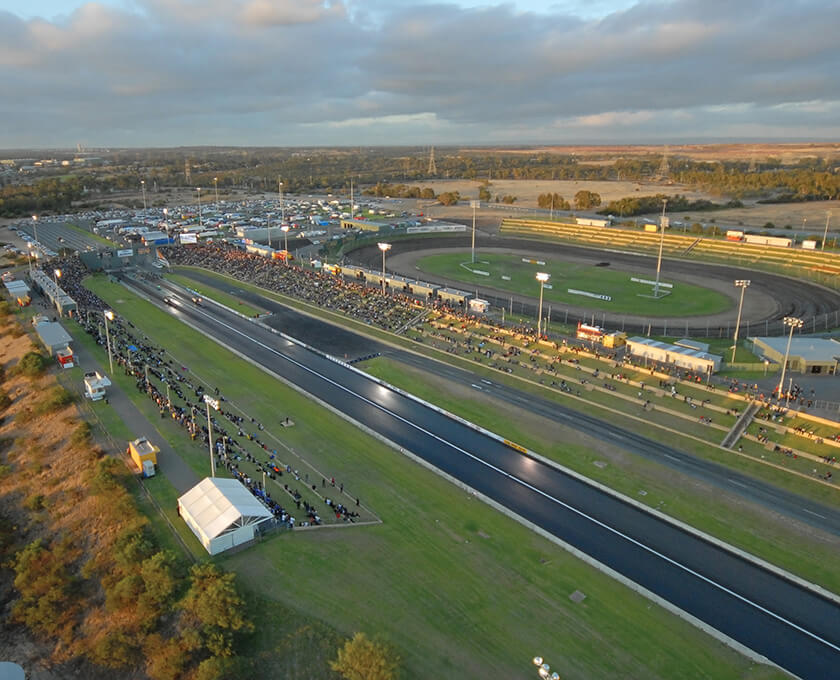
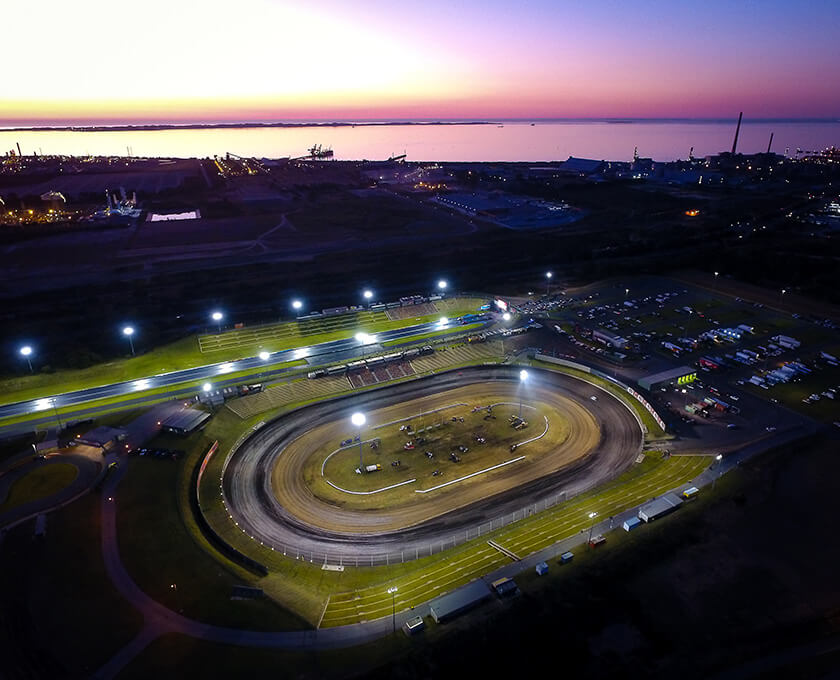
Early residue storage areas at our Kwinana Refinery were transformed into a hugely popular motor sport facility. The Motorplex attracts more than 275,000 visitors each year and is a success story for effective closure and completion.